Mold Release Wax, also known as Release Wax or Demolding Wax, is a specialized wax formulation designed to facilitate the easy release of molded or casted parts from their molds or patterns.
Composition: Release wax formulations can vary, but they typically consist of a blend of natural waxes, synthetic waxes, petroleum distillates, and additives. These additives may include agents to improve release properties, enhance surface finish, provide heat resistance, or increase durability.
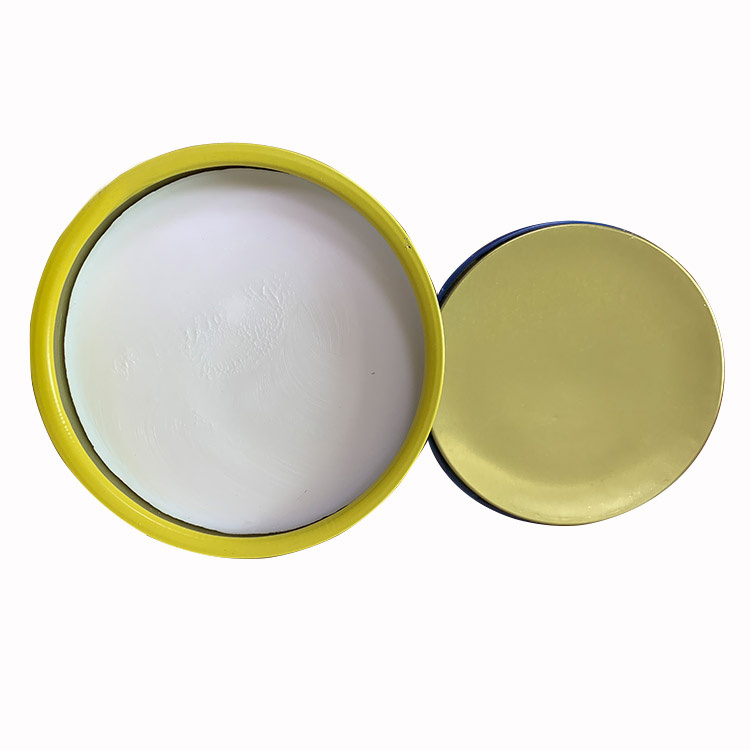
Types Of Release Wax
Carnauba-based: Carnauba wax, derived from the leaves of the Brazilian palm tree Copernicia prunifera, is known for its hardness and high melting point. Carnauba-based release waxes offer excellent release properties and are commonly used in applications where high temperatures are involved.
PVA (Polyvinyl Alcohol): PVA-based release waxes contain polyvinyl alcohol, which forms a water-soluble barrier between the mold and the casting material. After application, the PVA layer dries to form a thin film, which can be easily washed off with water after demolding.
Synthetic: Synthetic release waxes are formulated using a combination of synthetic waxes and additives. These waxes offer consistent performance across a wide range of temperatures and molding materials.
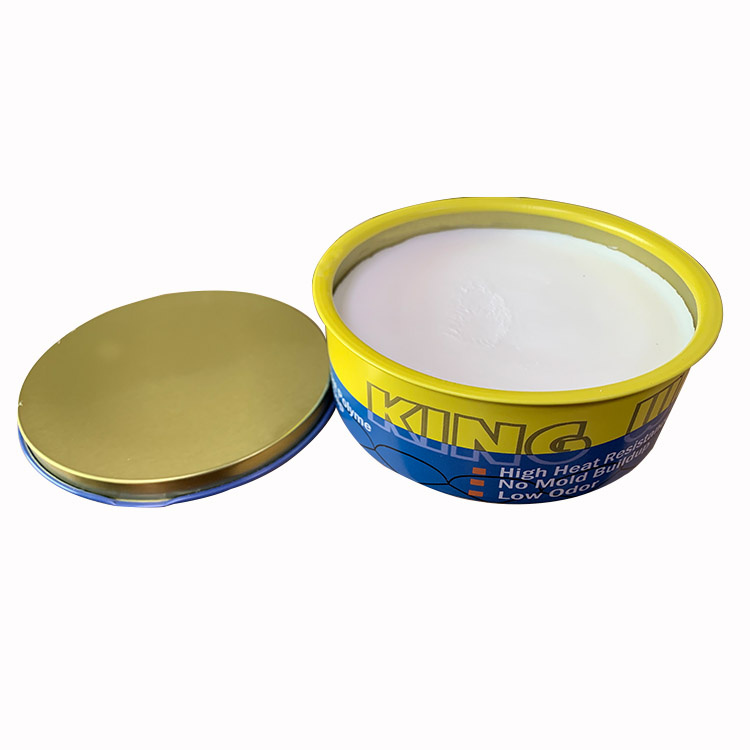
Our Release Wax
Application Methods:
Release Wax can be applied using various methods, including spray application, brushing, wiping, or dipping, depending on the specific requirements of the molding process and the type of mold.
Spray application is commonly used for large molds or when a uniform coating is required. Brushing or wiping may be preferred for smaller or more intricate molds.
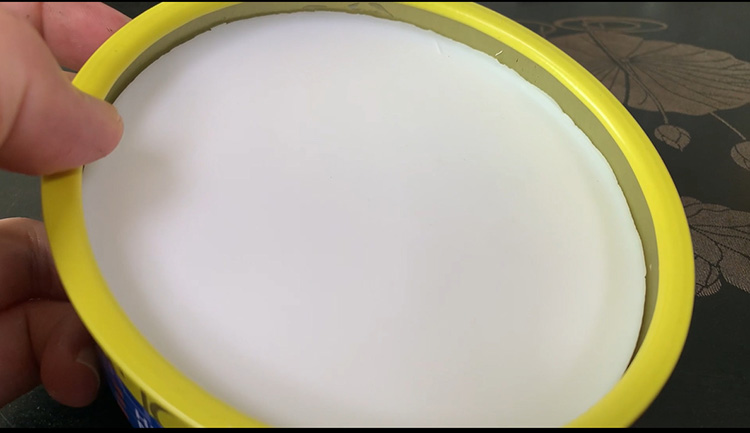
Product Details
Benefits Of Release Wax
Easy Release: The primary benefit of Release Wax is its ability to prevent adhesion between the mold and the casting material, allowing for easy demolding of parts without damage.
Surface Protection: Release wax forms a protective barrier on the mold surface, reducing wear and tear and prolonging the lifespan of the mold.
Improved Surface Finish: Release Wax can enhance the surface finish of molded or casted parts by filling in small imperfections in the mold surface and reducing surface defects on the finished parts.
Proper surface preparation is essential before applying release wax to ensure good adhesion and uniform coverage.
Compatibility with both the molding material and the mold material should be considered when selecting a release wax formulation.
Environmental and safety considerations should also be taken into account, especially regarding solvent-based Release Waxes.
Overall, Release Wax plays a critical role in facilitating efficient and high-quality molding and casting processes across a wide range of industries and applications.
How To Use Release Wax
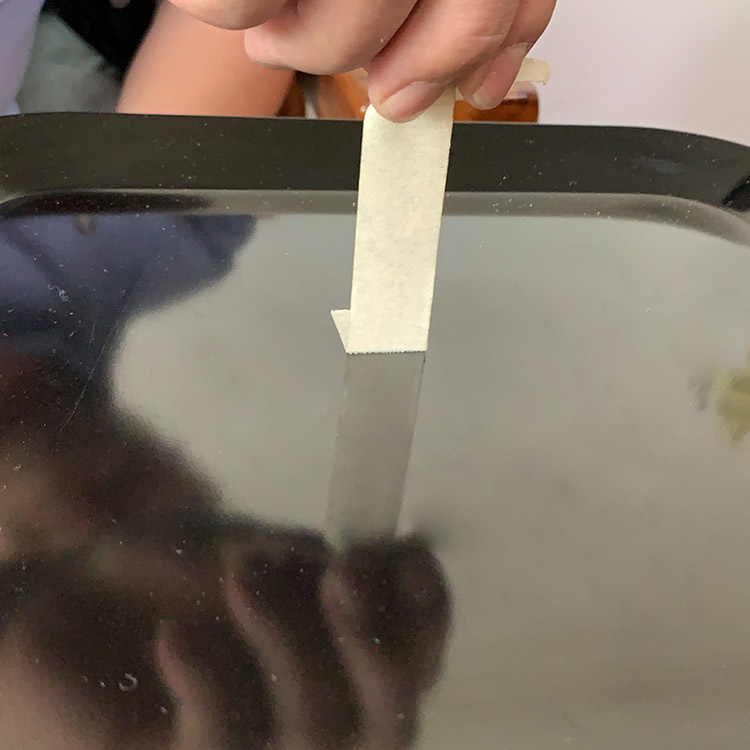
Effect Of Release Wax
Using Release Wax effectively involves several key steps to ensure proper application and optimal results. Here's a detailed guide on how to use release wax:
Materials Needed:
Using a clean, soft cloth or applicator brush, apply a thin, even layer of release wax to the entire surface of the mold.
Work the wax into any intricate details or crevices of the mold to ensure complete coverage.
Avoid applying too much wax, as excess buildup may affect the quality of the finished product.
Allow Drying Time:
Let the applied wax dry completely according to the manufacturer's instructions. This typically takes a few minutes to an hour, depending on the type of wax and environmental conditions.
Some waxes may require multiple coats for optimal results. If so, repeat the application process, allowing each coat to dry before applying the next.
Buff the Surface (Optional):
After the wax has dried, you may choose to buff the surface gently with a clean, dry cloth or buffing pad to enhance the smoothness of the wax layer. This step is optional but can help improve the release properties.
Molding or Casting:
Once the wax has dried and any optional buffing is completed, proceed with the molding or casting process as usual.
Pour or apply the molding material into the prepared mold, ensuring it fills all cavities and details evenly.
Curing or Solidification:
Allow the molding material to cure or solidify completely according to the manufacturer's instructions. This may involve waiting for a specific amount of time or subjecting the mold to certain temperature conditions.
Product Removal:
After the molding material has fully cured or solidified, carefully remove the finished product from the mold.
The release wax should facilitate easy removal, allowing the product to separate from the mold without sticking.
Clean Up:
Clean any remaining wax residue from both the mold surface and the finished product using a suitable solvent or cleaner, if necessary.
Ensure that the mold is properly cleaned and reapply release wax before the next use, if applicable.
Our Mold Release Wax have received positive feedback in practice. Contact us for further information on our products.
Contact Us:
Phone number:+8615823184699
Email: marketing@frp-cqdj.com
Website: www.frp-cqdj.com
Post time: Apr-22-2024